UV打印成品出現表面發粘、附著力差等問題,往往源于固化系統異常。這種現象在深色材料打印、厚墨層作業時尤為明顯,直接影響產品耐候性和商業價值。以下為典型故障排查指南:
1. 能量密度不達標:UV燈每使用800小時光強衰減15%,建議使用UV能量計定期檢測(標準值:透明墨水≥350mJ/cm²,白色墨水≥550mJ/cm²)。老化燈管及時更換,汞燈與LED固化系統需區分檢測標準。
2. 反射罩氧化失效:鋁制反射罩使用6個月后反射率下降40%,表現為燈管發熱量異常升高??捎苗R面檢測卡觀察光斑均勻度,出現條紋狀陰影需立即更換。建議選用鍍金陶瓷反射器,壽命延長3倍。
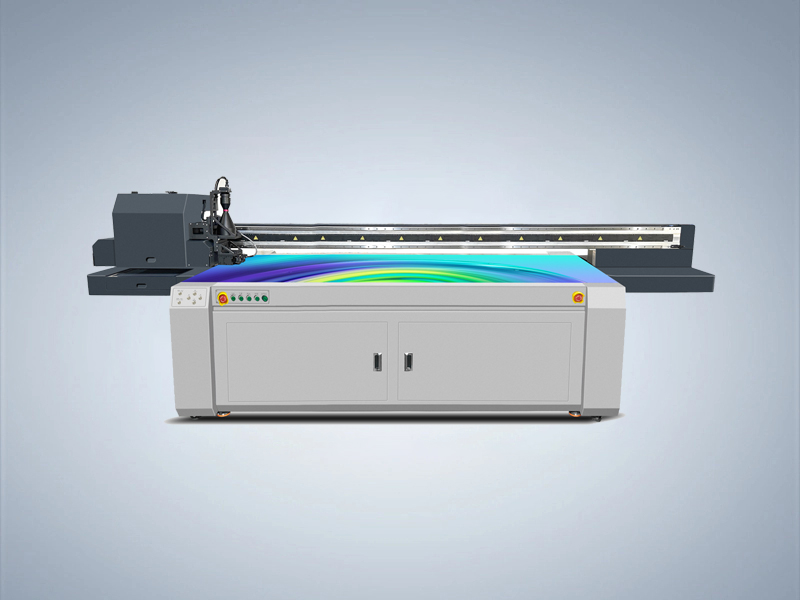
3. 打印-固化間距失準:介質表面與UV燈最佳距離為8-12cm。打印浮雕效果時,需同步調整固化系統升降機構,距離誤差超過±2cm會導致30%以上能量損耗。
4. 墨水透光率不匹配:打印黑色亞克力等吸光材料時,需選擇含光引發劑的深色專用墨水。第三方墨水建議做透光率測試,380-420nm波長透光率應>15%。
5. 冷卻系統異常:汞燈工作時溫度需穩定在700±50℃,采用雙循環水冷系統時,定期檢測冷卻液電導率(標準值<5μS/cm)。管路積垢達0.5mm厚度時,散熱效率下降60%。
6. 介質預處理缺失:PET、PP等非極性材料打印前必須進行等離子處理,達因值需提升至42mN/m以上?,F場可用達因筆快速檢測,未達標材料需返工處理。
建議每季度使用分光光度計檢測固化度,重點監控白色墨層的Tg值(玻璃化轉變溫度)。當出現局部固化不良時,可嘗試降低打印速度20%并開啟二次固化模式。通過建立能量-溫度-間距三維參數模型,可使UV固化效率提升至98%以上。